Integrated Injection Molding & DIP Material
Jun 07,2024
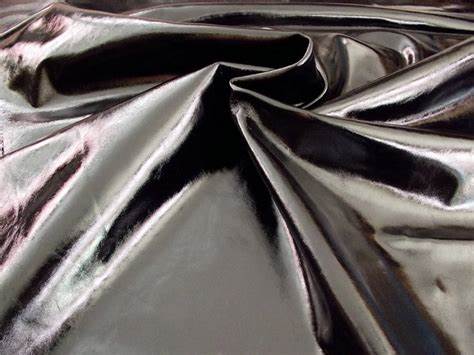
In recent years, the manufacturing industry has seen a growing trend towards the integration of different processes in order to streamline production and improve efficiency. One such innovative approach is the combination of Integrated Injection Molding (IIM) and Dual In-Line Package (DIP) material, which offers a range of benefits for manufacturers looking to enhance their manufacturing processes.
Integrated Injection Molding is a process that combines injection molding and assembly into a single operation. This allows for the creation of complex parts with multiple functionalities in a single step, reducing the need for additional assembly processes and minimizing material waste. By integrating these processes, manufacturers can achieve significant cost savings and improve overall productivity.
DIP material, on the other hand, is a type of material that is commonly used in electronic packaging applications. It is known for its excellent thermal conductivity, electrical insulation properties, and resistance to high temperatures. By incorporating DIP material into the injection molding process, manufacturers can create parts that are not only structurally sound but also offer superior performance in a wide range of applications.
One of the key advantages of using Integrated Injection Molding with DIP material is the ability to create parts with complex geometries and integrated features that would be difficult or impossible to achieve with traditional manufacturing methods. This opens up new opportunities for manufacturers to design innovative products that meet the demands of today's market.
Additionally, the integration of injection molding and DIP material allows for greater design flexibility and customization. Manufacturers can easily adjust the composition of the DIP material to meet specific performance requirements, such as thermal conductivity or electrical insulation. This level of customization ensures that the final products meet the highest standards of quality and performance.
Another benefit of using Integrated Injection Molding with DIP material is the ability to reduce the overall manufacturing footprint. By combining multiple processes into a single operation, manufacturers can save space on the production floor and reduce the need for additional equipment and machinery. This not only leads to cost savings but also contributes to a more sustainable manufacturing process.
Furthermore, the integration of injection molding and DIP material enables manufacturers to improve the overall quality and consistency of their products. By controlling the entire manufacturing process from start to finish, manufacturers can ensure that each part meets the highest standards of quality and performance. This level of quality control is essential for meeting the demands of customers and maintaining a competitive edge in the market.
In conclusion, the combination of Integrated Injection Molding and DIP material offers a range of benefits for manufacturers looking to enhance their manufacturing processes. By integrating these processes, manufacturers can achieve cost savings, improve efficiency, and create innovative products that meet the demands of today's market. With the ability to create complex parts with integrated features and superior performance, Integrated Injection Molding with DIP material is poised to revolutionize the manufacturing industry and drive innovation in the years to come.
PREVIOUS:
Contact Us
E-mail: salerelyon@gmail.com
Phone/WhatsApp: +86 15759875789
Address: No;40 7th Qianshan District, Neikeng Town, Jinjiang City, Quanzhou,Fujian, China