Rubber Foam Particles
Jun 07,2024
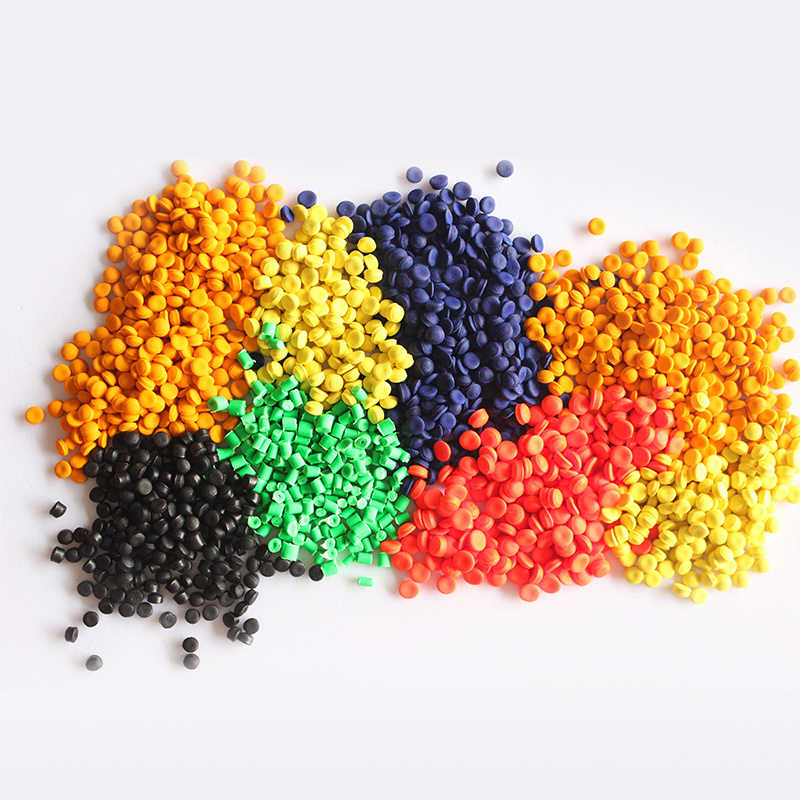
Rubber foam particles are a versatile material that has gained popularity in various industries due to their unique properties. These particles, also known as foam rubber or sponge rubber, are lightweight, flexible, and have excellent shock absorption capabilities. In this article, we will explore the uses, benefits, and manufacturing process of rubber foam particles.
Uses of Rubber Foam Particles
Rubber foam particles are widely used in packaging materials to protect fragile items during transit. The shock-absorbing properties of these particles make them ideal for cushioning delicate products such as electronics, glassware, and ceramics. Additionally, rubber foam particles are commonly used in the construction industry as insulation material. The closed-cell structure of foam rubber provides excellent thermal insulation, making it a cost-effective choice for insulating walls, roofs, and floors.
In the automotive industry, rubber foam particles are used in the manufacturing of car seats, headrests, and door panels. The flexibility and durability of foam rubber make it an ideal material for creating comfortable and long-lasting automotive interiors. Furthermore, rubber foam particles are also used in the production of sports equipment such as padding for helmets, knee pads, and shoulder pads. The shock-absorbing properties of foam rubber help reduce the risk of injuries during sports activities.
Benefits of Rubber Foam Particles
One of the main benefits of rubber foam particles is their lightweight nature. This makes them easy to handle and transport, reducing shipping costs for manufacturers. Additionally, foam rubber is a cost-effective material that provides excellent insulation properties, making it an attractive choice for a wide range of applications. The flexibility and durability of rubber foam particles make them long-lasting and resistant to wear and tear, ensuring that products made from foam rubber will have a longer lifespan.
Another benefit of rubber foam particles is their ability to absorb shocks and vibrations. This makes them ideal for use in packaging materials and sports equipment, where protection against impact is crucial. The closed-cell structure of foam rubber also makes it resistant to moisture, mold, and mildew, ensuring that products made from foam rubber will remain in good condition even in humid environments.
Manufacturing Process of Rubber Foam Particles
The manufacturing process of rubber foam particles begins with the creation of a foam rubber mixture. This mixture typically consists of natural or synthetic rubber, blowing agents, fillers, and other additives. The mixture is then heated and agitated to create a foam-like consistency. Once the foam rubber is formed, it is molded into the desired shape and size using specialized equipment.
After molding, the foam rubber is cured in an oven to set its shape and properties. The curing process typically involves heating the foam rubber at a specific temperature for a set amount of time. Once the foam rubber has been cured, it is cut into small particles using cutting machines or shredders. These rubber foam particles can then be used in a wide range of applications, from packaging materials to sports equipment.
In conclusion, rubber foam particles are a versatile material that offers a range of benefits for various industries. From packaging materials to automotive interiors, foam rubber has become an essential component in many products. With its lightweight nature, excellent insulation properties, and shock-absorbing capabilities, rubber foam particles continue to be a popular choice for manufacturers looking for a cost-effective and durable material.
PREVIOUS:
Contact Us
E-mail: salerelyon@gmail.com
Phone/WhatsApp: +86 15759875789
Address: No;40 7th Qianshan District, Neikeng Town, Jinjiang City, Quanzhou,Fujian, China