Materials Science Popularization | Foam Rubber Materials
Apr 23,2024
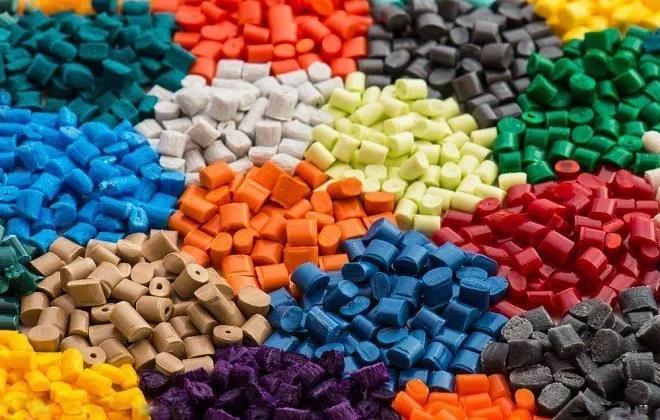
Foamed rubber is made from rubber as the base material and produced through physical or chemical foaming to obtain sponge like porous rubber structures. Foam rubber can be divided into three types: open cell, closed cell, and mixed cell, as well as low density, medium density, and high density. Due to its low density, elasticity, resistance to bending, shock absorption, sound absorption, and excellent thermal insulation performance, it is widely used in daily life and industrial products. Foam rubber, also known as rubber foaming technology, is a method of treating rubber with specific foaming agents to give it special properties, and is one of the most common methods in modern production.
Foaming principle
The principle of producing rubber sponge through solid rubber foaming is to add foaming agents and co foaming agents to the rubber material. After the foaming agent decomposes at the vulcanization temperature, gas is released to form foam pores, causing the rubber material to expand and form a sponge. The factors that affect the pore structure of the foam include the gas generation rate of the foaming agent, gas diffusion rate, adhesive viscosity, and vulcanization rate. Choosing the appropriate foaming agent and rubber vulcanization system is crucial. The vulcanization speed and foaming agent decomposition speed can be adjusted according to the vulcanization temperature, or the appropriate foaming agent particle size can be selected to balance the two speeds, in order to obtain the ideal foaming product. The vulcanization of foamed rubber can be achieved through either in mold free foaming or vacuum foaming methods, and the vulcanization temperature should be strictly controlled. The processing process includes various processes such as mixing, preparation of preforms, and vulcanization, and selecting the appropriate processing technology is crucial.
Matching characteristics
Main material selection
In the manufacturing process, scientific rubber materials should be selected, including natural rubber and synthetic rubber. For oil resistant foam products, it is necessary to choose appropriate nitrile rubber, analyze the proportion and relationship of chloroprene rubber, and even use multiple rubbers in combination. The plasticity of the rubber material is related to the density, pore structure and size, and foaming rate of the foamed rubber. It is advisable to choose rubber with good flowability and moderate Mooney viscosity as the main material to avoid low plasticity. A higher viscosity facilitates the dispersion of the compounding agent, resulting in foamed rubber with fine and uniform pores, good elasticity, and excellent shock absorption performance. The proportion is determined based on the comprehensive performance requirements of the product.
Selection of foaming agent
The selection of scientific and reasonable foaming agents is the key to producing high-performance foaming products, while also meeting the current social needs. At present, foaming agents are mainly divided into two types: organic foaming agents and inorganic foaming agents. Inorganic foaming agents decompose quickly and at low temperatures, but producing gases such as carbon dioxide and ammonia is not conducive to the production of closed cell foamed rubber. Organic foaming agents are widely used, with small particles and high gas generation, stable decomposition temperature, and easy production of foamed rubber with fine and uniform pores. They are also non-toxic, odorless, and non polluting. The properties of foaming agents such as gas generation, decomposition temperature, and shrinkage rate can be adjusted by adding foaming agents.
Selection of vulcanization system
In the research of foaming products, the vulcanization system is very important, and its matching relationship with the foaming system directly affects the performance of the product. Adjusting the matching between the curing system and the foaming system can be achieved by adjusting the foaming system after selecting the curing system, or adjusting the curing system after selecting the foaming system. The vulcanization of foamed rubber and the decomposition of foaming agents occur almost simultaneously, and the vulcanization rate should match the foaming rate. The sulfur vulcanization system has a slow vulcanization rate, and a combination of accelerators with fast vulcanization initiation and post effect accelerators should be selected to adjust the vulcanization rate. Peroxide vulcanization is also a commonly used vulcanization system, which has a slow vulcanization speed, a fast start, and is easy to control the vulcanization and foaming process. The decomposition temperature should be matched with the foaming agent. The vulcanization rate can be adjusted using the dosage of crosslinking agent.
Selection of fillers
Adding reinforcing agents such as carbon black and white carbon black can improve the strength and stiffness of foamed rubber products, while adding fillers such as calcium carbonate and clay appropriately can improve processing performance and reduce costs. Plasticizers need to have good plasticizing effects, rapid absorption, good compatibility with rubber, non volatile, non migratory, non-toxic, odorless, and cost-effective. The addition of plasticizers can improve dispersion, processing performance, and formability. For foam rubber products that require a high porosity, plasticizers with good compatibility with rubber and a large amount of addition should be selected. Due to the easy aging of foam rubber products, good anti-aging agents should be selected, and attention should be paid to not affecting the decomposition of the foaming agent. Antioxidants are generally used more than rubber products.
Main applications
Foam rubber products are a widely used product, which are divided into two types based on the different pores, namely microporous structure and porous structure. Microporous structures are further divided into individual foam products and continuous foam products. In addition, according to the different raw materials of rubber, foam rubber products can also be divided into various types, such as natural rubber foam products, isoprene foam products, SBR foam products, ethylene propylene rubber foam products, etc. This technology has been widely applied in products in fields such as automobiles, construction, sports, etc., such as door and window sealing strips, buffer pads, seismic resistant materials, etc.
PREVIOUS:
NEXT:
Contact Us
E-mail: salerelyon@gmail.com
Phone/WhatsApp: +86 15759875789
Address: No;40 7th Qianshan District, Neikeng Town, Jinjiang City, Quanzhou,Fujian, China